How to save costs when raw materials are scarce and prices are rising
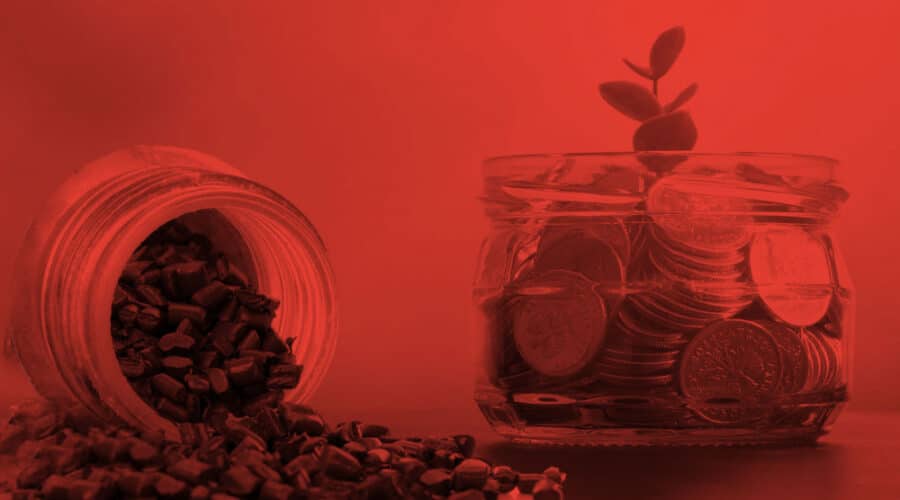
The snowball effect of the corona crisis
As I’ve already indicated above, the corona crisis is the cause of the problem — or, to be more precise, the starting point of the snowball effect of problems. The cost price per kg of raw material is determined by many different factors, and all these factors are connected to and strengthen each other. Below are a couple of examples of this.
Stagnant global economy
Due to the uncertainty about the course of the COVID pandemic, the global economy has been stagnant for some time. Especially at the start of the corona crisis, this produced a rapid decline in the demand for raw materials and caused producers to completely shut down certain production lines. And less production means fewer personnel and less inventory. Now that the economy in various sectors has quickly — too quickly — gotten underway again, many companies are beset by shortages in personnel and inventory.
Logistics problems
The lack of (healthy) personnel is also evident in the logistics sector. Containers of raw materials cannot be shipped (and returned) on time, which results in a shortage of containers and longer turnaround times, and eventually in rising transport costs. In essence, it is a question of supply and demand. The demand for raw materials continues to increase, while — due to personnel shortages or logistics problems — the supply is not growing along with it.
How can I save costs?
Limited availability, not enough personnel, longer turnaround times, and higher transport costs — all factors that increase the cost price of your product. Add to this the increasingly stricter sustainability rules imposed by the government. To save costs, it’s therefore advisable to take another good look at your own production process. Three opportunities form the basis of this review:
1. Choice of material: When there is a shortage of raw materials, recycled materials can be a solution if you have the equipment to process regrind at a low cost, such as can be done with our MCTwin configuration, for example.
2. Use of material: Use a dosing unit that works accurately so that you use precisely what is required and don’t waste (extra) raw materials.
3. Reduction of waste: Minimize rejects by simply working more efficiently with the right equipment.
Produce more efficiently
When raw materials are scarce, it becomes necessary to increase production efficiency. But if you produce high-quality plastic products, you’d rather not implement changes in the materials, or their quantity, that you use. It’s quite a challenge to keep an eye on the quality and your own margin when you are confronted with the problems outlined above. Why accurate dosing is the solution to these problems is explained by the following example:
Suppose you want to produce a red cap, pen, or pail of 97% virgin material and 3% color additive. Then you start searching for the correct ratio. At a certain point, you’ve found the right hue; you lock in the settings and you start production. The first runs go well but after a while the color starts to deviate toward a lighter tint.
The operator sees that the additive percentages are fluctuating between 2.5% and 3.5% and decides to increase the standard percentage to 4%, to achieve the correct (darker) hue. That may seem logical, but it also means that the material use will standardly be 101%. In short: 1% of material will be wasted in each run. This is something that will cost thousands of euros annually, but it also results in rejection and an additional impact on the environment.
Accurate dosing: we’ll help you!
To avoid waste, rejection and (extra) environmental impact, you must therefore manage your material use more accurately by dosing accurately with the right dosing equipment. These are processes that we deal with every day. We do that with our proven gravimetric dosing technology, which ensures that your product will look precisely as set in advance. It also provides insight into how much of each component you use, or how your product is actually constructed.
Would you like to learn more about our dosing technology and products? Then have a look at our product page or complete the form below for a free consultation with one of our dosing experts.